Advancing training in propagation
By Dan Austin
It is an uncertain time for the future of many industries, horticulture included. As the greats of old, age and retire, quality training is needed like never before. So, in an industry that is increasingly moving online, it is fantastic when training providers invest in much-needed material assets.
No two nurseries are exactly the same. Whether it is a difference in location, topography, or even water quality, while one nursery may appear to have perfected production, duplicating the same design elsewhere may not deliver the same outcome. When looking at establishing educational nurseries, successfully adopting the positive aspects of existing nurseries requires even more consideration, and forethought, as the area becomes a teaching space rather than a profitable production facility. This is exactly what has been happening recently at TAFESA’s Urrbrae campus.
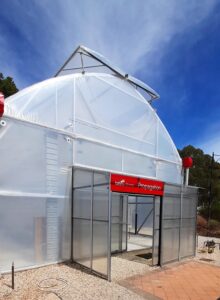
In a rare opportunity, the campus was given funding to replace its aged and degraded propagation facility. So, staff set about visiting propagation nurseries across the state to see what was working and what wasn’t. Ecodynamics Nursery at Penfield Gardens produces hundreds of thousands of native plants vegetatively, using bottom-heating foil mats with bench tops slightly angled downwards to avoid water pooling on the mats – a top tip taken on at Urrbrae when replacing its dated sand propagation benches. On a visit to the Mount Lofty Botanic Gardens Nursery, staff observed the use of individual cloches over heat beds which allows for greater control over specific species needs, or propagation techniques, as well as irrigation and heat having a minimal impact on the environmental conditions in the rest of the greenhouse; another tip adopted in the new facility.
The heat beds in the new house are thermostatically controlled and the irrigation scheduling for each one can be controlled independently based on either time or temperature. This is a great feature, allowing staff and students to tailor watering to the stage of individual plants, and a significant step forward from the previous system that irrigated the entire propagation area using a single balance arm sensor.
Wet wall cooling was observed across several nurseries but rather than best practice, this appeared to be due to affordability, and the budget for this project allowed for the installation of a fogging cooling system along with automated energy screens and gull-wing ventilation. Although the budget allowed for a fantastic facility, it didn’t quite stretch to fitting the greenhouse out with twin-wall polycarbonate, which would have been the ideal option for appearance and longevity. Instead, an inflatable dual-skinned house was negotiated.
The structure was constructed on a lined gravel base, with all water runoff able to be captured and processed through a wetland water purification system. Initially, it was thought that this project would also include the replacement of a neighbouring polytunnel used for hydroponic growing, and as a result, white Reflecta Mat was selected to surface the floor of the facility. This surface maximises light and is valuable in cropping situations, although the permeability of the product is less than other surfacing materials used in water capture systems, so time will tell how this performs.
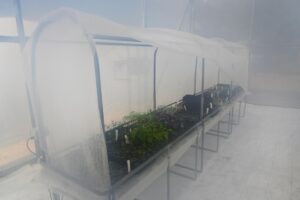
The first cuttings were struck in late March, and it is still early days for the facility, but the plants are moving along well. The structure has also stood up to its first significant wind event. Wind speeds that brought several trees down in the area also led to a power cut, and without power the inflatable dual-skin hung loose and deflated as the wind wore on. Staff were gritting their teeth and preparing for the worst, but no damage occurred. Fortunately, the house’s wind sensors had instructed the gull-wing vents to close before the power went out.
Taking the best part of a year, from the demolition of the old house to the completed construction of the new one, it has been a long wait, but given the potential benefits for the future of training in propagation, it has been well worth it.
Dan Austin
IPPS Member, Author
Lecturer, TAFE South Australia
M: 049 122 8591
E: daniel.austin@outlook.com
Main photo: The new propagation facility is designed to maximise light