Hang it all
Save space. Cut labour. More profit.
By John Fitzsimmons
With the growth of apartment living, with more balconies and courtyards, and more awareness of the possibilities for 3-dimensional greenscapes indoors and out, it should come as no surprise that hanging baskets are a growing category. While specialist growers have been doing baskets for a long time, economic pressures and technical innovation have produced a range of options to improve productivity and quality.
For some nurseries hanging baskets are their sole focus – their ‘bread and butter.’ For others they are an adjunct line – an opportunity to broaden their offering, meet seasonal demand, and/or increase the dollar return from each square metre of production facility (green- or shadehouse). In addition to the usual growing knowledge and skills there are some more particular aspects of hanging basket production that can be noted. These include species selection and basket size/s. Combination baskets usually include species that perform well under similar growing conditions, e.g., temperature, fertility, growing media and pH.
Combinations of plant forms that produce the ‘thriller-filler-spiller’ effect, or that combine into mounding and trailing habits, or that burst into colour, or produce contrasting or complementary textures forms, are all popular templates.
Growing media characteristics and pH are also key considerations. Avoid plant combinations that prefer broadly divergent media and pH conditions (a pH range of 5.6 to 6.2 is one recommendation); selections that are less pH sensitive help meet this challenge.
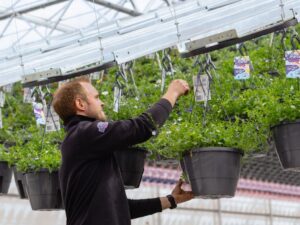
It can be several weeks between transplanting and raising the baskets to elevated positions in the green- or shadehouse. During this pre-elevation period is when residual (slow or delayed release) fertilisers are added, and residual pest and/or disease preventative treatments are made.
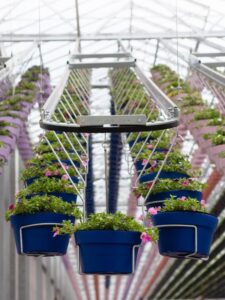
Then it’s up to an optimal growing zone with (hopefully) even temperatures and humidity, and good access to appropriate natural light. Of course, provisions should be considered for watering, progressive inspections during the growing period, and any remedial actions that might be needed such as re-planting, trimming or pest/disease treatments.
Depending on the scale of production, various approaches can be taken from high labour-low capital cost startups to high productivity-capital intensive facilities. Plant or basket volumes and labour requirements are vital criteria. The ultimate weight to be borne by elevated systems must be factored in, as well as how irrigation needs will be met. Consider also whether baskets will be suspended over walkways or clear floor, or whether a system will be employed that permits parallel use of the floor area below – and how will the baskets get up there?
At the simplest level, hanging baskets can be produced with available labour, hooks and a step ladder (WH&S notwithstanding). Many owner-operators consider this as ‘normal’ with the ultimate profits (if any) providing the return on their own labour inputs. But as many farmers who previously welded their own farm gates ultimately recognised, while minimising cash flow ‘out’, this was not really utilising ‘free’ labour, and the savings or returns, or ‘opportunity cost’, were not necessarily worth it.
Obviously when using paid labour there is a more identifiable cash cost to the basket hanging activity. For arithmetic’s sake let’s assume minimum wage plus on-costs (superannuation, holiday pay, leave loadings etc) at $30 per hour or $0.50 per minute. How many ‘pick up baskets, walk to the spot, climb the ladder, hang the basket, climb down, go back and get more baskets’ can a worker do each hour? Then there’s the reverse when the crop is ready for sale, and maybe some remedial treatments or trimming along the way. The question is one of productivity and production cost even if it’s not a daily or even weekly task. Two or more workers increase productivity but logically increase overall labour costs.
Pots, baskets or benches on the floor also compromise access and therefore hanging space.
Traditionally, hanging baskets over aisles spreads the input costs per square metre of building and therefore contributes to potential profit margins. Trolleys might reduce the ‘walking transport’ costs especially in large houses.
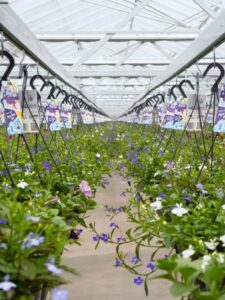
Next, let’s consider a real world modest 300m² (10m X 30m) grow house, perhaps with two longitudinal walkways separating three rows of benches. Perhaps about 500 baskets are suspended (manually) in 10 rows above the walkways at around 500mm intervals. Irrigation is provided by way of fixed lines along the rows of baskets, with individual sprinklers or emitters for each basket. Each line is fed via individual filters and manual valves at the end of the house (so) any one line of 50 positions can be turned on or off depending on whether baskets are present or not. Timing is manually controlled. At this scale it’s simple, it works. But it is still labour intensive and lacks versatility in terms of any part-rows or baskets at different stages of growth across rows. Perhaps a simple programmable irrigation control would help.
So, thoughts turn to other measures.
Scissor lifts provide elevation and (some) longitudinal mobility combined with some basket transport capacity. Depending on power and drive system, platform lift height, wheel or track type, manoeuvrability, origin and new or used status these machines can be very affordable to rent and around the price of a used car (say, $14,000-plus) to buy where justified. Just remember safe operation, operator training, regulatory compliance (where indicated) and any operator licencing required depending on jurisdiction.
Depending on the structural design and strength of the growhouse, travelling gantries suspended from the ceiling across the production areas below or running along alley ways and extending across floor level production areas, can provide a next level option. They may provide a way to hang larger numbers of baskets efficiently and safely, while increasing the potential growing area at floor or bench level. Depending on dimensions of growhouse and gantry they might also provide added amenity – for husbanding lower plants from above with less area lost to walkways, or carrying irrigation/fertigation or lighting systems serving the lower plants.
Which brings us to the concept of basket conveyor systems. Depending on type and complexity this idea has been around for one or two decades. However, like many things these days, developments in computer power, programming and control have evolved an existing basic idea into systems far more advanced in terms of versatility, flexibility and capacity.
If the labour needed to load/unload and husband the baskets is significantly reduced or eliminated by mechanisation then a major production cost has also been reduced in a dramatic way. Manual handling and effort are minimised and walking and carrying all but eliminated. Irrigation and other plant husbandry actions can also be minimised to as little as one point – the baskets are brought to the water and/or treatment.
Some systems are best considered at the greenhouse design and construction stage. Others are readily retrofitted or adapted to existing or readily modified structures. The ultimate weight of a fully loaded system is obviously a major consideration. This can vary significantly according to the size, number and spacing of hanging baskets, the baskets’ irrigation status and stage of development. If it is engineered, designed and installed appropriately then the productivity benefits can flow.
Broadly there are two types of basket conveyor systems – cable, and chain.
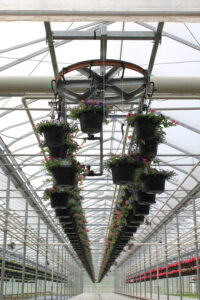
more light gets through to plants at ground or
lower levels (Image Cherry Creek Systems)
In chain drive systems, typified by the designs from Metazet of The Netherlands, plants are supported on hooks or carriers fixed on a chain enclosed in a track. The track is usually suspended from the growhouse frame. Basket spacings can be varied by where the hangers are placed on the chain. Usually the end of the track/s can be lowered allowing basket loading and removal at ground level.
Several advantages are claimed by the chain system including:
- less tensioning and stretching issues with chains, which can result in smoother less ‘juddery’ operation. The mounting and tensioning arrangements required for cable systems can (depending on design) also introduce undesirable ‘inward’ tension forces on the growhouse structure, especially the end or side elements.
- chain systems can make left and right (‘inside’ and ‘outside’) turns, as well as go up and down over obstacles such as grow benches, electrical control boxes, irrigation or other infrastructure etc. Cable systems are usually limited to straight line ‘down and back’ parallel return systems. This means chain systems offer far greater flexibility in layout. There is often an associated benefit of fewer drive motors with less electrical wiring and switching being required.
- Metazet’s chain system utilises rigid suspension points for smoother operation and less stress on the building structure.
The chain system also usually incorporates a section that is lower, or lowered, for loading and unloading, inspecting or trimming/treating, baskets from floor level. This is a major source of operating cost savings especially of labour, and of the need for hire or purchase of ancillary equipment like scissor lifts, ladders or gantries.
With any suspended basket system irrigation/fertigation can be confined to as little as one point – the plants delivered to the water not the water taken to the plants. Delivery to passing baskets can be via nozzles, showers or funnels. Most watering systems can be mechanised and programmed according to climate control parameters, plant species, media moisture content, zonal requirements or other criteria. Consistency and uniformity are important.
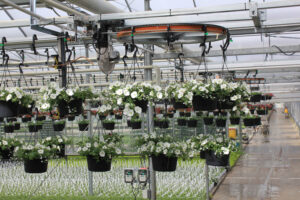
The cable type often has baskets suspended on a returning cable running the length of the growhouse, in the style of a ski lift. The cable/s run around a large diameter drive pulley or ‘drum’ at one end and an idler pulley/drum at the other end of the system. The cable is supported and carried over pulleys from above at appropriate intervals. Basket spacings can be made as required and, optionally, hanging baskets at different heights effectively provides multiple levels for species with different light requirements or at different stages of growth. Makers of cable systems often cite less light interruption to plants below as an advantage (compared with belts or other more substantial structures); this is also a common debate between various greenhouse frame designers. Examples of cable systems are the Echo installations from Cherry Creek Systems of the USA.
There are various options, but, as one example, Cherry Creek Systems focuses on its core strength of the cable mechanical systems. However, they are happy to work with experts in environmental control to better model and match conditions, and crop requirements, utilising the growhouse’s other facilities – shade systems, fans, heating and cooling, venting, etc. Their controllers are therefore designed to be compatible with familiar environmental control systems including Argus, Priva, Wadsworth, Q-com, and others.
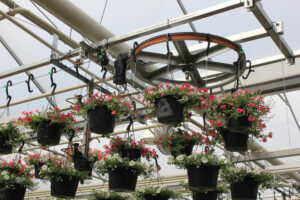
Many basket watering systems deliver water to the plants based on Vapour Pressure Deficit (VPD). This is the difference between the amount of moisture in the air and how much moisture the air can hold when it is saturated. Once air becomes saturated, water will condense on the leaves; this makes the plant more susceptible to diseases including rots. Conversely as VPD increases the plant needs more water. By some guidelines plants grow best with VPD around 0.85 kPa in the range 0.8 – 0.95 kPa.
Summary
Labour is a major cost in nursery production. Where productivity can be maintained or improved, reducing labour costs can contribute to profitability. Mechanisation and automation can save on labour and boost productivity. Especially in the growing category of hanging basket production, growing at scale with minimal labour may improve returns on investment. Contemporary versions of established concepts are well worth consideration, and with some being highly versatile, flexible and readily retrofitted to existing growhouses, there is potential for significant increases in production off existing floor areas.