Machinery and green infrastructure
By Michael Casey
Green Infrastructure installations are fast becoming an inclusion in our cities as we work towards finding solutions to mitigate the negative effects of climate change.
These installations, located around our cities, appear on rooftops, sides of buildings, within tight spaces, and in locations that makes the installation and maintenance of green spaces much more difficult than what we commonly install at ground level.
As we devise ways of how to safely build these green installations, we as an industry can agree that the knowledge and the advances in technology of machinery and safety accessories has ensured that machinery employed at various stages of green infrastructure projects is safe and beneficial to us all.
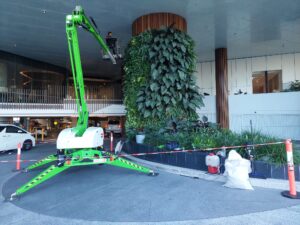
The following article will look at the machinery and safety technologies in, and on, the built environment, as most ground-based installations such as swales, rain gardens, urban landscape installations utilise the same types of machinery used throughout the conventional areas of landscape installations.
Construction and site preparation of green spaces onto and into buildings has posed many new challenges, and has designers and installers turning to companies specialising in equipment suited to moving, lifting, and shifting large items into the spaces reserved for green infrastructure.
Cranes, often seen lining our cityscapes, placed high above the building have been one method for the safe movement of materials and equipment onto the work site. This machinery, referred to as a tower crane, has become an essential tool in assisting urban landscapes to become a reality through the safe transporting of plants and trees, along with building materials, to roof spaces and balconies on high rise buildings, and ensures labour costs are kept down, and more importantly, protects the safety of the worker.
Manual handling of supplies, as mentioned previously, has been improved with the use of on-site machinery and lifting mechanisms. Manual handling of materials has been a major cause of soft tissue injuries throughout the construction industry for some time, with a reported 24% of serious claims in 2021-22 coming from lifting, pushing, pulling, or bending (Australian Bureau of Statistics). The construction industry, through improved safety standards and guidelines and with the use of more machinery and lifting tools on site, has assisted the industry to reduce these numbers.
The uses of soil ‘blow in’ companies has literally taken the backache out of moving soil/growing media around work sites. Soil and mulch blowers are generally diesel-powered machines available in trailer or truck-mounted configurations, that disperse mulch where it’s needed. An interior conveyor and air lock system feeds the mulch in the hopper into a hose, where high powered air delivers the mulch wherever the operator places the hose. These companies have the ability to blow in mulch, soil, or stone to any part of a building or site and can reach the tops of structures all through the set-up of pipes connected back to the main truck. The use of these machines has assisted in numerous ‘hard to reach’ green space installations and takes the hard work out of moving vast amounts of materials onto buildings. Projects can now be installed quickly, and with reduced labour input have resulted in a safer and timely turnaround on deliverables, along with freeing up staff to perform other tasks on the site and minimising the risk of fatigue and injury.
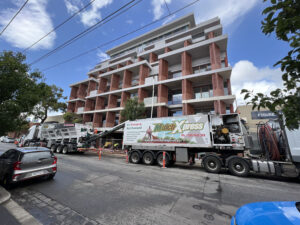
Maintenance and monitoring of installations post construction is a critical part of the success of any green infrastructure installation. Once construction has ceased, the ability to access roof spaces, green walls, and balconies becomes difficult with building occupancy governing what can and cannot move through a building. Trying to navigate plant replacements or materials replacements through or onto a building when access and machinery has disappeared, will be extremely difficult.
As mentioned in previous articles, I have written about designing with maintenance in mind to ensure that in post construction there are solutions already in place to ensure the ease of maintenance and replacement of materials.
To understand more about what machines and safety technologies are used by green infrastructure maintenance firms for the maintenance of these installations, I spoke to Mitch Clouton from Fytogreen and Drew Burns from Evergreen Infrastructure. Both highlighted the many various types of machines available and what is required for maintenance works, with Burns noting that “When confronted with the use of varying machinery needed to service and install these projects (scissor lifts, spider booms, scaffolds, and BMUs (swing stages)), they are not easy skills to master, and can be quite confronting learning at 40 stories up in the building canopy of cities. These challenges continue when you imagine 25 km/h gusts that pop up out of nowhere as you are halfway down the building. We must acknowledge the skill our teams possess, and the professionalism they hold while completing these challenging and dangerous tasks.”
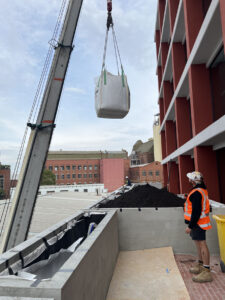
Mitch Clouton from Fytogreen also adds that “Ground machinery like knuckle-booms, spider, or scissor lifts, are effective ways to reach difficult positions – however, getting these large machines in place, and isolating a safe work area is often difficult. Naturally, this type of machinery requires a certified driver, and the preliminary costs of this access mean that the number of maintenance visits is minimised to remain cost-effective.”
The many machines and technological advances for maintenance companies has made working in these environments safer and easier. Elevated Work Platforms (EWP’s) now come in many sizes and shapes allowing for tight access while still reaching heights. Boom and knuckle lifts allow for access for height and hard to reach areas while conventional scissor lifts still play a part in granting access to our installations.
After speaking to Burns and Clouton, they both reiterated several times about the need for an understanding of the site and the available EWP’s on the market, and to ensure that the correct machine be specified for that job. Both noted that access to buildings via foyers (where a lot of these green walls and installations are found) meant that tight access and ability to set up in tight and often busy foyers, meant machines needed to provide more functions than the earlier conventional models such as scissor lifts.
When machines are not an option, rope access has now become a familiar sight with specialists working both inside and outside on green infrastructure installations. The ability for rope teams to gain even better access to exterior garden planters than machines, has ensured our designers can push the boundaries for where they specify these green spaces.
On the topic of heights and rope teams, the once familiar Building Maintenance Unit (BMU) has become a familiar tool for green infrastructure maintenance companies needing to reach balcony gardens. At a much cheaper rate for the building owners, these machines can ensure costs are managed with varying trades using the building installed maintenance unit to wash windows, maintain green infrastructure, and general building maintenance.
What must be understood about maintaining, installing, and accessing these sites is that all works are carried out in most cases at height, in tight spaces and locations, and most importantly in areas that all require relevant training and skill set. Working at heights requires a specific ticket (Working at Heights certificate) along with relevant machinery training to ensure people understand how to use the many technologies and machines on the market, the latter coming in the form of an Elevated Work Platform certificate. Both skills require training that is provided by many Registered Training Organisations (RTOs) around the country and is a requirement when working on these sites. Rope access training to become a certified rope technician is also available through many RTO’s, while the training to use BMU units is often completed with the building manager and the company that supplied the unit.
Our industry is changing and the many new forms of green infrastructure installations is both pushing the boundaries while providing some exciting visual installations. These all require, as mentioned, an understanding of the machines that will assist us as installers and maintainers of green spaces in the built environment. Smart use and knowledge of these available options will ensure successful outcomes, and more importantly reduce injuries to staff and others.
Michael Casey, Director of Evergreen Infrastructure
and MJC Horticulture
Advisor to the green infrastructure industry.
E: michael@evergreeninfrastructure.com.au
Main photo: Scissor lift in action maintaining a city green wall (Image: Fytogreen)