Issues in the design, build and relocation of a native plant nursery
By David Hancock
This article outlines some of the issues associated with managing the forced transition of a unique business from one site to another and the challenges associated with that project.
It is rare for these circumstances to arise, and this case study can rest not only as a guide to others in a similar situation but also when considering a complete site relocation.
It is accepted that the move provided the opportunity to reconsider and upgrade the nursery business, enhance propagation facilities for efficiency, and improve staff working conditions.
The following provides details relevant to this business but has clear relevance for others when considering a new facility.
General information on the challenges, design, specifications and outcomes, as well as a conclusion summary, is also provided.
The endemic plants of Western Australia are recognised worldwide for their unique floral attributes within the biodiversity hotspot of the southwest of the State.
The Natural Area nursery business, which is part of the Natural Area Holdings environmental businesses, has developed over the last twenty years to be renowned for its capability to propagate a wide range of endemic Perth and southwest native plant species, including many considered difficult/recalcitrant to propagate from seed. The nursery produces over 500 Perth and WA regional species, and over 90% from seed.
The family-run business, Natural Area Consulting Management Services, operated from a long-term government-leased site at Whiteman Park in Western Australia commencing in 2005. Over 15 years, the nursery area quadrupled in size, producing 80,000 to 800,000 tube size stock.
Piecemeal expansion over those years led to fragmented logistics, with three separate nursery areas across a tight and disjointed area.
In January 2020, and coinciding with the arrival of COVID-19, the State Government advised that they required the entire site for a new train station complex for a rail line. We were being forced to relocate and needed to exit the site by the end of 2021, which gave us less than two years.
Almost a year went by while searching for a new site, negotiating for relocation, negotiating rebuild compensation, appointing an engineer and designer, and finding building companies for the works.
A new site 4 km distant, and within Whiteman Park, was finally agreed in early 2021. The huge task of managing the existing nursery, and simultaneously project managing the new nursery construction, was underway with a 12-month deadline.
The works were undertaken during extreme labour shortages and material supply delays due to COVID-19 impacts. Despite the Government driving the requirement to move, we faced the frustration of dealing with multiple agencies for planning, heritage, environmental, transport, and services. The new site had no services, and new installations for power, water, and communication were necessary.
In the very early stage, we had initially hoped to time our relocation to late winter/spring of 2021, but the time taken to deal with all the preliminaries meant that we were facing a stock relocation in late 2021 – early 2022, with high stock levels and at peak production in the heat of Perth’s summer.
New nursery design
The new nursery design and specifications achieved were a game of endless brinkmanship. The Government was only committed to replacing like-for-like, but it required that we project manage the entire build and relocation. An enormous amount of management time was involved, effectively taking 1 FTE (full-time equivalent) staff time for 1.5 years. The demands on the nursery team were extreme, but the prospect of a much better work environment and nursery facilities drove them on.
We chose a bitumen hardstand for all the traffic areas of the nursery to allow for forklifts and heavy vehicles, and deep compressed blue metal aggregate for the growing areas. The buildings were spaced to allow machinery and trailers adequate room to access the propagation area. The growing program remains essentially the same as the old nursery but with enhanced space of approximately 35%, which was a good result and well above like-for-like. The design allows for readiness and expansion to the west. Some propagation houses were built to our proven design, with others of a more specialist type by Argosee Greenhouse Technology. The buildings were located on-site according to the best logistics, and the manner and frequency of access.
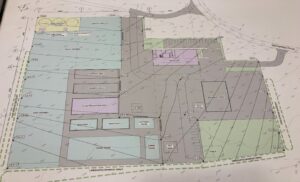
The stock transition in January 2022 was difficult in 40ºC-plus heat. Losses in stock and production time were high, and no compensation was available. The staff did an amazing job. It took four trucks and four forklifts ten days, and most of the company workforce, to get it done.
The new nursery has superior water quality and systems, and enhanced production facilities for staff and stock.
The outlook for the 23/24 season was much improved on 22/23, but the move adversely affected stock and sales shortfalls.
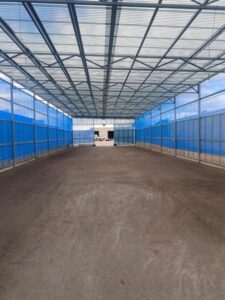
The current year’s production target of 1.3 million plants has been achieved to overcome the transition downturn.
The site design has allowed the use of imported Combi Trac all-terrain forklifts and small 4×4 converted ride-on mowers connected to trailers for improved plant movement, which was not available to us on the old site. The new covered growing areas provide a wide range of propagation conditions.
The production shed has insulated walls, doors and roof, with modern conveniences that provide a quality work environment.
Nursery – Summary of specifications
Water supply – Onsite groundwater bore with automated supply to storage tanks.
Bore water is filtered via Netafim F6000 with clay-based media to remove solids and reduce the iron level to below 1 part per million. Automatic backwash water supplies a seed production area.
Water storage – 960 KL in 3 x 320 KL steel tanks, independently filled. Storage is for cover in the event of bore pump failure.
Irrigation system – 4 x Grundfos CRE 20-4 variable pressure pumps, each on consecutive demand, delivering up to 80 Kl per hour. This is sufficient to water the entire outside nursery area at one time if required.
The nursery is watered by station selection based upon plant needs and to minimise power draw, watering in daylight hours to suit 30 kw solar power system output.
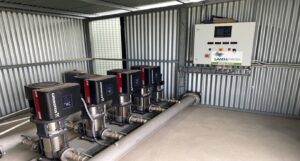
Service water via Grundfos constant pressure jacking pump to 25 watering service points across the nursery.
Post pump filtration – Netafim screen guard at full pressure with 120-micron mesh (1.5 human hair width) and automatic backwash water to supply seed production area.
Irrigation control – Signal SDS 50 system operated by remote cloud app to adjust station start and run times, and monitor pump pressure.
Willowbank Frost Watch Environment System is set to operate a short-run irrigation cycle at 1ºC and lower.
Emergency power system backup – hard-wired generator to bore and irrigation system.
Bermad Solenoids and Netafim Orkal disc filters to fine spray overhead irrigation areas.
Outside growing areas – 14 stations supply 300 Netafim Gyronet turbo-rated 160 litres per hour at 5.5m rests at 3 bar.
Growing capacity – Currently approximately 1.4 million tubes.
The shade house is 1000m² and has powered retractable top and side screens. It has overhead irrigation with Netafim Spinnet 90 litres per hour at 4 metre rests, operating at 4 bar.
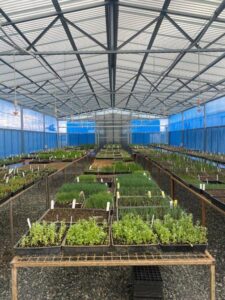
Seed propagation houses
2 x 200 m² enclosed houses with differing polycarbonate roof finish for light and heat control variation. One house has 48% light transfer and 32% heat transfer; the other has 26% light and 50% heat.
Overhead irrigation with Netafim Spinnet at 90 litres per hour at 2 metre rests at 4 bar. Our design for Perth conditions.
Palletised growing areas/auto seeding – 2 x 350 m² with differing polycarbonate coverings: one at 48% light transfer and 32% heat transfer and the other at 26% light and 50% heat. Overhead irrigation with Netafim Spinnet at 90 litres per hour at 2 metre rests at 4 bar. Our design.
Cuttings propagation house – double skin polycarbonate 200 m with automatically controlled light, temperature and humidity. Conventional and LED lighting. Envirostep control system. Overhead Netafim Coolnets 7.5 litres per hour at 1.5 metre rests, 4 bar. Supplied by Argosee.
Tunnel house – 250 m² poly film. Powered retractable overhead and side shading. Netafim Gyronet turbo at 160 litres per hour at 3 metre spacings. High water output for hotter conditions. Supplied by Argosee.
Plant production shed. 800 m² single span insulated roof with Bondor double insulated panels to doors and walls. Air-conditioned office and break-out kitchen/lunch area and wet areas. 7 x 4 m sliding doors to facilitate drive through machine movements.
Nursery Equipment
Kanga mini loader. Combi Trac all-terrain forks. Heli HD forklift. 2 x Kubota 4×4 ride-on with twin 4-wheel steer trailers. KW auto seeder and conveyors. Urbinati tray filler. Weather station monitored by phone.
Soil bins – 3 x 30 m².
Conclusions & learnings
The new design has given rise to substantial efficiency gains in the region of 30% production growth for equivalent staff costs. The additional machinery has relieved the staff of much manual lifting. The composite site design has avoided the productivity loss that applied to the old site, which was effectively three separate nursery areas & systems. The new site is level, safer, and faster to traverse. The location of the nursery manager’s office relative to the main nursery growing areas allows frequent visual access to nursery conditions and stock presentation. The gain in efficiency has allowed the creation of a new staff member role built around monitoring of growing and stock conditions, SOP’s, water management and maintenance, allowing the nursery manager to concentrate on sales, production planning and people management.
New systems have been established to monitor/adjust water usage relative to nursery digital weather station recordings. The new site’s orderliness has made stock checks, stock takes, and despatch much more efficient.
We were surprised at the different site weather conditions after a 4 km move, driven by reduced bushland wind mitigation. The new site is more open, and the hardstand in the new nursery increased the heat effect on some nursery areas. It took a full season to understand and adjust.
The improvement in water quality resulting from improved filtration has markedly improved plant quality and survival rates.
The irrigation control via a phone app has allowed the nursery to dispense with weekend and holiday monitoring, resulting in significant savings and staff benefits.
Staff now enjoy working and break time conditions to a high standard, and have been enthusiastic in assisting with the continuous improvement of the new nursery.
David Hancock
Founder & Consultant
Natural Area Holdings Pty. Ltd.
All images supplied by Natural Area Holdings Pty Ltd