Minimising waste in micropropagation
By Lisa Wightwick
Efforts to reduce waste are on the rise across many industries worldwide. However, in a line of work where success and productivity hinge on using many single-use products, is it possible to reduce waste?
Do you remember seeing the vast amounts of waste produced by hygiene-related items, such as masks and gloves, during the pandemic? Unfortunately, when things need to be kept sterile, there’s limited to no capacity for reusing or recycling. The same can be said for plant tissue culture, where sterility is critical to overall success, and many products used are single or limited-use consumables with the potential to create vast amounts of waste.
Plant tissue culture (PTC) and micropropagation (using PTC to mass-produce clonal plants) must occur in sterile conditions. The nutrient and sugar-rich media in which TC plants are grown are also ideal breeding grounds for enterprising little fungal spores or bacteria that may find their way in. Cultures can be rapidly overtaken by contamination, often resulting in severely compromised plant health or mass destruction of entire batches. To prevent this, PTC laboratories utilise equipment, products and procedures that all contribute to maintaining sterile conditions. Many of these products are single-use items, such as examination gloves, paper towels and shoe covers, and frequently replaced consumables including cleaning products and plastic takeaway containers. Some commercial micropropagation laboratories can produce enough of this waste to fill skip bins on a weekly basis, often disposing of recyclable and non-recyclable items together.
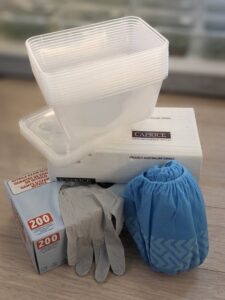
In the plant propagation industry, a considerable volume of waste is also produced when large quantities of new plants are produced. My laboratory is no exception to this, although the baseline of waste created is reasonably low, I still wanted to find ways to reduce it. Fortunately, my job allows me the perfect environment for contemplating new ideas and the liberty to test them and put them into practice. I began to think about ways to reduce waste that were accessible and practical. Balancing the eco and economic is a fine art, especially in the context of commercial production. Changing a process or product to a more environmentally friendly option is great, but it can sometimes come at a cost, financially and productivity-wise.
One of the biggest waste generators in micropropagation is the plastic takeaway containers that house TC plants. Large commercial operations can go through hundreds of thousands of these per year, as the containers are generally single-use and degrade over time through exposure to sterilising treatments, prolonged exposure to light and heat, and general mechanical handling. Because the containers are filled with chemically-laden gel media and biological matter (plant and microbial), it can be difficult, impractical and sometimes unsafe to separate the contents from the plastic in order to recycle it. High turnover facilities would have to constantly expend significant labour emptying the containers so they can be disposed of responsibly. It’s easier and cheaper for these businesses to throw it all into a dumpster, and sadly this happens pretty often. I can understand the necessity of being efficient and economical. I too use plastic takeaway containers as they are cheap, space-saving, non-fragile and easily procurable. However, there’s no excuse for poor waste disposal practices where no alternative has been explored.
I’ve investigated the possibility of using glass vessels over plastic, which can be an excellent reusable alternative, but realistically, changing over to glass would be too expensive and complicated for a small facility like mine. Washing and sterilising glass vessels would need to occur regularly, which still consumes energy, water and labour. Additionally, most glass TC vessels are small and quickly outgrown by the plants inside, increasing the turnover rate and the required washing and sterilisation.
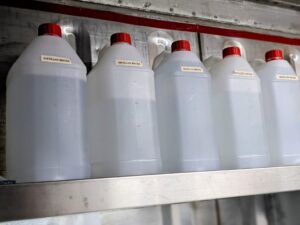
Single-use plastic or reusable glass are two options at opposite ends of the scale, one benefiting efficiency and budget, but harmful to the environment, and the other better for the environment, but more labour-intensive and costly. Not finding either viable, I found a more realistic and achievable option – the sacred middle ground. I replaced a portion of plastic containers with glass for strategic use in housing small amounts of plants with long shelf lives. Despite drawbacks that would impact large-scale production, there can still be a compromise where glass vessels are implemented in a more specific area where such drawbacks are negated.
Although the supplementation of glass vessels was a good step, I still sought a sustainable solution for the disposal of the plastic containers, which account for the majority of use. The containers could be emptied and placed into the recycling bin, but a better solution arose. After an enlightening tour through Garden City Plastics and learning about the PP5 recycling initiative, I asked if I could include my emptied containers (which happen to be made from PP5) in the red collection cage that our facility uses typically for spent nursery trays and pots. The answer was yes! Instead of going into the domestic recycling bins, where they may or may not end up recycled, they go straight to a local facility where they are broken down and remade into usable products. The additional labour it takes to empty and stack used containers is minimal, only adding about 30 minutes of work, once a month, if that. Even with this recycling process in place, I only dispose of containers when they are absolutely at the end of their life and have implemented process and scheduling strategies to minimise turnover of cultures.
I found many other novel ways to reduce my laboratory waste, like thoroughly washing and repurposing old chemical or cleaning product bottles. Empty 5L ethanol bottles are perfect for storing distilled water (required for many aspects of PTC). Instead of buying new spray bottles, they can be sourced from used-up cleaning products (please note: mixing chemicals can be extremely dangerous, and care must be taken to meticulously remove any residual chemicals). Disposable shoe covers can be replaced with silicone sneaker covers or a pair of clean shoes specifically for laboratory use. Gloves can be used multiple times as long as they are intact and haven’t been used to handle anything contaminated. Carboard boxes and bubble wrap from incoming deliveries are saved for reuse when shipping out stock. Essentially, if something can be reused, I’ll reuse it.
By combining this array of ideas and techniques, the waste output of my laboratory has significantly reduced, only generating one medium bin liner-full per week. For a yield of 115,000 plants per year, a single bin-bag is not too bad, considering that’s about the same as a domestic household creates. Some of my waste-saving ideas may likely be regarded as radical by general standards, but reconsidering existing procedures and protocols, and conducting careful and sustained testing has undoubtedly yielded positive results. I’d encourage anyone wanting to reduce waste to consider the following:
- Lateral, novel and innovative thinking
- Challenge preconceived ideas and procedures
- Stay open to new or alternative options
- Test different products and methods
- Balance cost and productivity with sustainability
- Seek accessible and realistic alternatives
Sustainability is an investment. The cost doesn’t have to be high. Small investments add up over time. Aiming for realistic, achievable changes will ultimately have a much greater chance of success. It’s not always viable to choose the most expensive or labour-intensive option, even though the benefits to the environment may be greater. Finding the middle ground, like I did, is a valid path, which still had a very positive result.
Please contact me or scan the QR code for an expanded list of techniques and ideas for increasing sustainability in plant tissue culture laboratories.
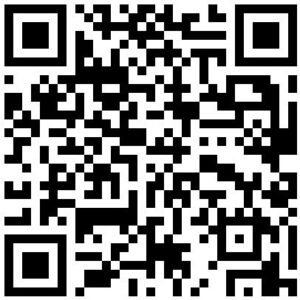