How do we work with robots?
By John Fitzsimmons
Artificial Intelligence (AI) and robotics are real world considerations for horticulture these days. While there are several drivers of the trend where do we, as humans, sit in the considerations?
From a purely economic or business perspective the development and adoption of robotics is often considered a ‘no brainer’. Machines are cheaper than humans, work longer hours, take no breaks, don’t get sick or complain – don’t they? One of the closest everyday examples are automated checkouts at supermarkets and other retail stores but humans have reacted to this development in different ways. Some have accepted or embraced it, others have taken their business elsewhere to continue a human relationship with its service and social advantages. Even in supermarkets, a hard core of customers still queue up at the reduced number of manned checkouts for various valid reasons.
Nevertheless, automated technology doesn’t always arrive cheaply, usually needs continuing maintenance, adjustment and updating. And there can be significant investment costs in integrating such technologies into existing physical, administrative and technical environments.
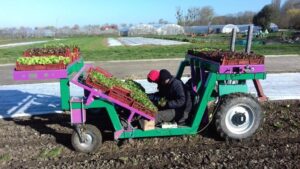
An interesting large-scale example was recently reported involving the mining industry. This is a sector that is still very much based on the real physical world – digging stuff up, processing it and moving it around the planet to where it is ultimately utilised. To date, that has largely been based on human effort and mechanical aids – digging, boring, processing and moving. Mining sites are often in remote areas requiring expensive logistics for people, tools and equipment, and resources (such as water and fuel or energy). By definition it can be dangerous work for humans and economics usually demand large economies of scale. A recent BBC report described the mining company Rio’s use of driverless vehicles, including 300 tonne tippers and water carts that carry around 160 tonnes of water just ‘to settle the dust’. There are reportedly about 2000 such driverless machines now working around the world, a population that has reportedly grown four-fold in the last few years; about 50 in one fleet alone on one Western Australian mine site.
By taking humans out of the situation on the ground has obviously improved safety, and productivity gains have been reported. The BBC report says no jobs have been lost as a result of this development; many former drivers have been re-trained as remote ‘controllers’ and for other roles. One controller reportedly looks after up to 20 autonomous trucks in relative comfort and safety 2500km from the mine site.
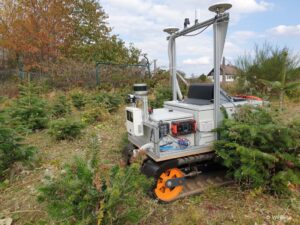
But even the manned versions of these vehicles cost several million dollars each and the real cost of the automation, monitoring and control is not readily available. The systems are not perfect, with occasional issues reported involving identification of potholes and wet, slippery sections of road – and their ramifications – to be remedied or reduced. Nevertheless, in the mining example, the balance appears to favour the safety, productivity and cost saving of automation.
In that scenario the stakes, economic and human, are high, so evaluation, monitoring and improvement are constants. There remains a need for on-site workers and the autonomous systems to be aware of each other. Controllers should not be overloaded and their concentration abilities exceeded. Information and user interfaces should similarly be designed for use and interpretation (and responses) by humans.
The BBC report said Professor Robin Burgess-Limerick, who studies human factors in mining at the University of Queensland, observed “The designers of the technology should put a bit more effort into considering people”. There were also considerations of ‘over-trust’, where people become so confident the autonomous equipment will stop that they start putting themselves at risk, which can become an issue.
In horticulture the stakes might not be as high as in mining but can have significant impacts on individual enterprises nonetheless.
As an example, early automated cherry colour sorting equipment had difficulty distinguishing between varietal extremes of colour and shape. Depending on variety, location and season, cherry colours range from almost black through dark red and bright red to creamy or light pink. The shape of cherries also varies with variety from somewhat ‘squat’ to round and heart-shaped. So, over time, the imaging technologies and software of automated sorting equipment has had to be continually improved and tweaked to meet a wide range of use situations. Earlier equipment also often needed operation with ‘cluster cutters’ because it worked better with single fruits than the clusters often delivered to the pack shed from hand pickers in the orchard. This is a simple example of the additional costs and considerations often associated with automation.
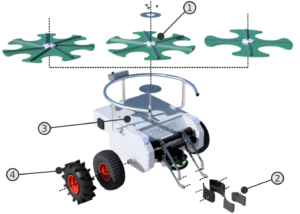
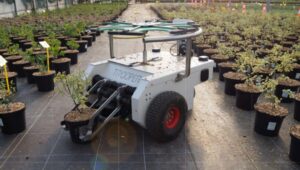
Automated fruit size and quality grading equipment has progressed rapidly. In one of Australia’s more advanced automated pack shed’s sorting systems each individual piece of fruit is imaged 80 times or more before being graded, handled and packed according to colour, size, shape and blemish. Near infra-red (NIR) scanning is also employed to make sure we are delivered tasty fruits like pineapples with enough sugar (sweetness) to meet customer expectations.
In ornamental horticulture major propagators have long used advanced automated systems to sow and germinate seed, evaluate germination and emergence, grow, pot-up and physically manage inventory. Examples include Boomaroo, Withcott, and Ball. These operations are positioned in very high-volume production sectors where major cost savings in labour and greater productivity (per labour unit and per square metre) are quickly justified and achieved. For smaller enterprises the opportunities for automation can be identified but not always so readily exploited or financially justified.
Nevertheless, with the rising cost and scarcity of suitable motivated labour for simple physical nursery tasks the opportunities are growing and the solutions don’t always have to be matters of high finance and bewildering technology. Simple transport and watering robots are starting points.
Consider the Trooper from Instar robotics of France now available in Australia through Hortiquip. The concept is as simple as things get. This machine moves potted stock from one place to another – for example from a high-density growing situation to a lower density growing-out or hardening-up area, as instructed. Inputs are minimal but a lot of labour such as lifting and carrying can be eliminated.
Mechanically the Trooper is also simple. It has drive wheels on one axle and swivelling castors behind. The ‘robot’ simply identifies where it needs to go and moves forward and back, or pivots, into position as required. A simple lifting arrangement, like a mini front-end loader, is fitted at the ‘front’. This grabs and lifts, or retrieves and deposits pots one at a time on to an onboard carousel that rotates to present an empty position (or a loaded pot to deposit) as required. Early prototypes were made of wood and worked with just 3 pots. Now the Trooper is a finished product handling up to 7 pots at a time (depending on pot size).
Such a basic concept can be scaled up and evolved further, resulting in a versatile autonomous worker such as the Innok Heros from Germany (also represented by Hortiquip). Promoted as ‘one robot – many faces’ Innok’s Heros is a modular robot that can be assembled according to client requirements and is expandable and convertible having 3- and 4-wheeled configurations with a wide range of attachments and superstructures possible. It can carry loads up to 400kg. Battery life is up to 16 hours and recharging can be done in 2 hours.
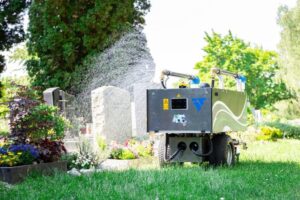
Heros’ applications thus far have ranged from herbicide spraying to watering, doze-load-carry-unloading of mass materials, and warehouse trailer-train haulage. The ROS (Robot Operating System) software is capable of mapping, obstacle avoidance, autonomous navigation or following people, following marked lines and area processing.
The Rainos variant has been designed to water ornamental areas such as cemeteries. It self-fills at plotted points, taking on 215 litres of water in about one minute and dispensing up to 20,000 litres per day! Operating mainly at night, an onboard camera has also proven an effective security device and deterrent against intruders, theft and damage. Rainos has been in use now for 3 years.
Another unit from this company, Induros, is focused on logistics environments. It weighs about 165kg, can tow up to 700kg, charges up in 2 hours and can work for up to 16 hours with its 48 Volt 2900 Watt hour battery. It is designed to work over a range of surface conditions from smooth indoor finishes to rougher outdoor conditions. Induros also boasts innovation in that it can locate itself and navigate its tasks indoors and out using a combination of reference systems in common application scenarios, such as in production or logistics spaces, in open or vegetated outdoor areas, in tunnels or underground. Innok calls this Hybrid Navigation™.
Induros also has an option where it is fitted with an onboard roller table for carriage (and subsequent unloading) of items that are delivered and/or accepted via roller conveyors common in many logistics and sorting installations.
The software behind these technologies should have certain features that allow adaption to desired tasks, improvement and updating and, of course, good functionality in the use situation. Desirable features include ‘openness’ and cross platform functionality and support, the versatility to use large or small robots, and the ability to adapt to both 2- and 3-dimensional operation spaces. Obstacle avoidance, human, non-human, stationary and mobile, is all but a given for safety and efficiency; also think back to the mining example of wet roads and potholes in the earlier mining scenarios.
Consider also a robot’s ability to know that entering new unplotted spaces, around corners or through doorways as examples, is ‘unknown’ and therefore speed, direction and ‘awareness’ may need to be varied ‘intelligently’ to gain knowledge of the site and situation, and avoid undesired outcomes.
Robots connected to the Cloud also allow remote technicians to quickly respond to concerns and promptly investigate and interpret the current status of the robot, update a system’s software or help reset it for changed requirements. Such connections can also help predict maintenance requirements based on the analysed data.