Productivity elements for successful growth
By John Fitzsimmons
Just what are the most common tools and structures used by successful greenlife growers? A visit to Boomaroo Nurseries outside Geelong in Victoria during the recent IPPS conference generated much interest and provided a useful site as a basis for discussion of such ideas.
In almost any industry, enterprises operating at large scale are often admired, respected, and emulated. It’s not necessarily for everyone or every vocation, yet the means of achieving success at scale still provides valuable lessons and guide posts.
First you need to be very good at the basics of the enterprise, be they production or service. Then you need the people and resources to achieve that. It was summarised well by Mike Hindle, part owner of another major greenlife operator – Queensland’s Withcott Seedlings in a business interview: What makes your business successful? “The quality of our plants and the team that supports that quality.”
The one piece of advice he would give to someone starting up a business is “Get your team right.” He regards the highest achievement to date as “giving our customers the confidence they will get the best possible product.”
What better or more succinct objectives would you want for your enterprise? Sustainability is also now a major factor in planning. Reliable supply of inputs like energy and water can also be big consideration depending on location. Recent events have tested logistics networks – for inputs, staff, and delivery to market/s.
But how can this be achieved at scale? Assuming you have the team and skills right, you need the desire and the resources. Not everyone wants to get big or has the ability to handle scale. If you do, then it’s down to financial and technical resources. The first rests largely on your performance to date and is between your accountant/s and backers.
The second, when considering equipment and technologies, is that it is beneficial to partner with supplier/s or service providers who can meet your needs and expectations in the medium to long term. They can also help you plan and steer growth en route to your goal/s. If one partner doesn’t offer a complete package then several suppliers can be chosen, as long as they integrate effectively and complement each other.
For example, a supplier of growing media should work in harmony with a plant nutrition consultant. For the same reason, suppliers of automation systems should offer technologies and mechanical systems that work together and are easily expanded or modified to suit future plans or changes in enterprise needs.
Automation or mechanisation is where you can have many benefits. Such systems usually work longer hours more reliably than humans, and often deliver on two highly valuable greenlife quality factors – uniformity and consistency.
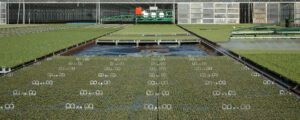
Look – no hands!
Large scale enterprises especially use automation at the propagation stage to closely and accurately monitor and control temperature and humidity. Computing power and speed can now povide complex calculation and control at surprisingly low relative cost.
Common mobile and wireless communication can now also make installation, and subsequent changes to equipment composition and layouts, easier and cheaper, in addition to the more commonly touted ‘control at distance’ benefits.
Mechanisation also makes possible the physical handling of very high quantities of seedlings safely and with little or no human effort. This can include the storage and supply of trays to seeding equipment, the delivery and management of growing media to trays, and the movement of trays in and out, or through propagation zones.
Automated placement of seeds in cells, and subsequent detection and remediation of failed germination cells is now the norm in many propagation operations. It is not possible for manual performance of this process to anywhere near equal the speed (rate per hour or day), accuracy, and consistency of the technologies available today for these tasks. The cost benefits are also uncontested when seedling volumes are in the hundreds of thousands or millions per year as they are at Boomaroo, Withcott or Ball.
Going undercover
A plant’s terrestrial environment can be as important as what goes on in the rootzone. Most propagators and growers know this and utilise various overhead structures. However, the advantages of highly evolved protected (cropping) systems are seeing rapid expansion of highly engineered structures using advanced new materials, and rapidly advancing climate control systems for light control or delivery, temperature, humidity, and air quality and movement.
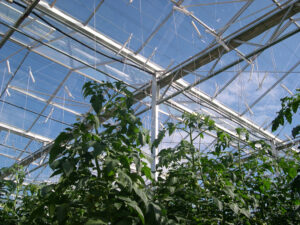
As examples, building/glazing materials that generate power for the enterprise’s operation, that react and respond to changes in temperature and light intensity, are becoming part of the real world and not confined to laboratories or fiction writing.
Advances in the understanding of plant physiology and metabolism, now being linked with advances in electronics, physics, chemistry, computing and artificial intelligence (AI), are making much of what was once imagination a reality. Of course some limitations – of specific crop information and wider cost-benefit remain. But the real-world possibilities are expanding fast.
With concerns about energy costs (and reliability, and sustainability long term) much heightened in very recent times, the nursery’s energy systems are no longer a simple matter of paying electricity or gas bills. There are options. While not in the greenlife sector, a number of pig and poultry enterprises have converted their own animal wastes into energy. In at least one documented case the payback on the investment in change (admittedly with the benefit of some government incentives) was about two years! That enterprise no longer pays an electricity company upwards of $250,000 a year.
Consider the benefits of collaborating with such an enterprise that might produce an energy surplus! (See below)
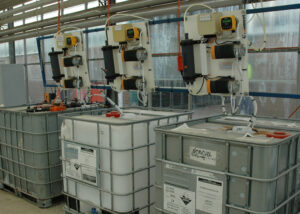
Nutrients and water
While drought years are in the rear vision mirror for many greenlife enterprises (not all), the need to supply an adequate, reliable water supply of suitable quality remains high.
The relationship between water and plant nutrients has always been close because solubility is associated with uptake. This is just one reason liquid nutrients applied through fertigation are popular. Other good reasons include reduced labour requirements and WH&S factors.
Several large scale greenlife operations previously had to source, store and then mix raw (plant nutrient) materials before application to the plants. That involved purchasing administration, logistics, manual handling, and warehousing, with commensurate human resources, building and equipment costs. They now leave those matters to a trusted* supplier who simply delivers liquid nutrient mix/es in bulk volumes to required schedules. Unloading then becomes a fast and simple matter of connecting a hose, and feeding the plants becomes a fast, simple, and safe matter of opening a valve (manually or automatically). No manual handling, no chemical storage challenges, and less warehousing and administration.
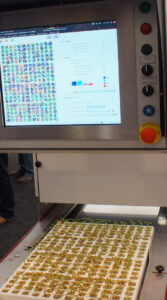
*Where a grower uses a patented or customised nutrient formula, perhaps from a specialist outside consultant, the confidentiality and integrity of the nutrient supplier is also important in the choice.
Action above and below
Most production nurseries are now familiar with moveable benches. But how is that built, powered, and achieved? And, at scale, how does that relate to the movement of greenlife across larger sites and maybe through several production zones? Smaller enterprises might still use manual handling and trolleys, larger ones stillages and fork lifts. On a higher plane again, overhead gantries can be justified for serious volumes. Or what about floor-embedded guidance tracks and autonomous transport systems. Endless slow speed belt systems the length of the greenhouse have been used for production of fast-growing crops (e.g. salad leaf or hydroponic lettuce) with plants harvested or redirected as they arrive at the end of that section. Hort Journal Australia has also reported on the use of small robots to move plant pots around, saving time, labour, and reducing the risks of manual handling injuries.
Could your enterprise benefit from a logistic productivity lift?
Go cubic
Land is not cheap and utilisation therefore needs to be optimised. Traditionally, greenlife has been produced on just one level or plane. However, a number of systems have emerged in recent years that utilise multi-level modes of production. One system rotates trays of plants like a supermarket chicken rotisserie. Others have multi-layered growing levels each serviced by grow lights; this is a fast-growing technology sector (no pun intended). Productivity per square metre is multiplied significantly.
Integration and cooperation
As competition for suitable land increases the pressure to use land area more productively and efficiently, there are more reasons emerging for integration and cooperation between complementary enterprises. Think aquaculture and hydroponics as an example. One produces nutrient as a waste product that can be utilised by the other.
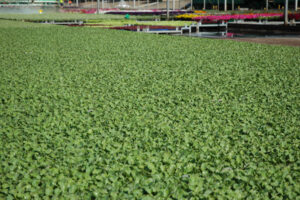
Global networks
Such ideas as those above come to life where there is a need and require an innovative mindset to implement. They also need evolving and adaptable networks of knowledge and resources. This might be more achievable, certainly at scale, beyond the traditional ‘hands-on’ business structures of our greenlife industry.
As an example, an English investment fund recently became a partner in Withcott Seedlings. This brought with it financial resource and management expertise for an enterprise producing hundreds of millions of seedlings each year. However, it also introduced Withcott to a broader international network of technology investments. It is expected this development will lead to “enhanced application of technology and robotics to improve production efficiency, such as the automation of seeding, sorting, grafting, monitoring, watering, and feeding.” It is reported that initial steps in this direction have already been taken by the company, which has previously introduced ISO Robotics (another company in the investor’s portfolio) propagation robots into its production with positive results in product quality and efficiencies.
Main photo: Robots are increasingly saving labour performing even menial tasks in nurseries
(All images supplied by John Fitzsimmons)